Product Lifecycle Management Plm Definition Benefits History
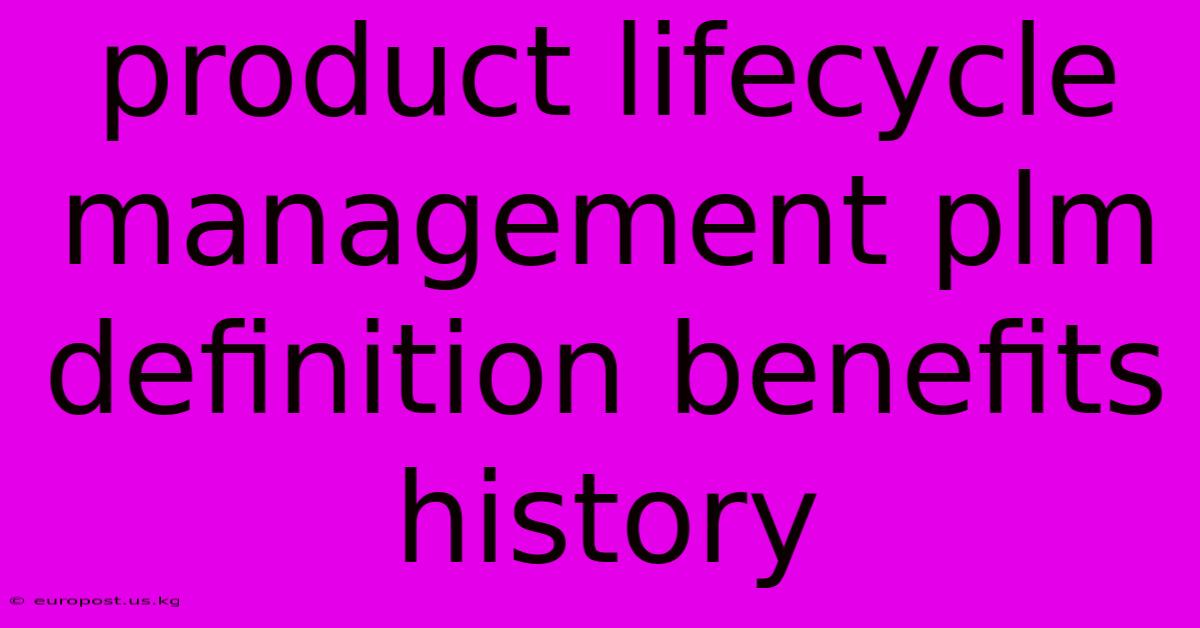
Discover more in-depth information on our site. Click the link below to dive deeper: Visit the Best Website meltwatermedia.ca. Make sure you don’t miss it!
Table of Contents
Unveiling the Secrets of Product Lifecycle Management (PLM): Exploring Its Pivotal Role in Modern Manufacturing
Introduction: Dive into the transformative power of Product Lifecycle Management (PLM) and its profound influence on product development, manufacturing, and overall business success. This detailed exploration offers expert insights and a fresh perspective that captivates professionals and enthusiasts alike.
Hook: Imagine streamlining every stage of your product's journey, from initial concept to end-of-life disposal, with unparalleled efficiency and collaboration. That's the promise of Product Lifecycle Management (PLM). Beyond simply managing data, PLM is the strategic backbone for innovation, cost reduction, and market leadership in today's dynamic landscape.
Editor’s Note: A groundbreaking new article on Product Lifecycle Management (PLM) has just been released, uncovering its essential role in shaping modern manufacturing processes.
Why It Matters: In today's fiercely competitive market, bringing innovative products to market quickly, efficiently, and cost-effectively is paramount. Product Lifecycle Management (PLM) provides the crucial framework for achieving this, integrating all aspects of product development into a single, unified system. This deep dive reveals how PLM streamlines workflows, enhances collaboration, and ultimately drives business growth.
Inside the Article
Breaking Down Product Lifecycle Management (PLM)
What is Product Lifecycle Management (PLM)? PLM is a strategic approach that manages the entire lifecycle of a product, from its conception and design through manufacturing, distribution, use, and disposal. It involves integrating various business functions and technologies to create a single source of truth for all product-related information. This includes design data, manufacturing specifications, quality control information, and lifecycle cost data. Think of it as a central nervous system for your entire product development ecosystem.
Purpose and Core Functionality: PLM's core purpose is to optimize the entire product development process, improve collaboration, reduce costs, and accelerate time-to-market. Its functionality encompasses several key areas:
- Requirements Management: Capturing and managing all requirements related to the product, including functional, performance, and regulatory compliance needs.
- Design Management: Managing and controlling product design data, including CAD models, simulations, and specifications. PLM systems facilitate version control, change management, and collaboration amongst design teams.
- Manufacturing Process Management: Integrating design data with manufacturing processes to ensure smooth production, minimize errors, and optimize efficiency. This includes managing bill of materials (BOMs), production planning, and quality control.
- Supply Chain Management: Connecting with suppliers and managing the flow of materials and components throughout the supply chain. PLM systems enhance visibility and transparency, improving procurement and logistics.
- Service and Support: Managing product service, maintenance, and support operations, including tracking warranty claims, managing spare parts, and providing customer support.
- Data Management: PLM systems provide a central repository for all product-related data, ensuring data accuracy, accessibility, and security.
Role in Sentence Structure: While not directly related to grammatical sentence structure, PLM's impact on communication and data organization is significant. PLM facilitates clear and concise communication across departments, eliminating ambiguity and ensuring everyone is working from the same information. This streamlined communication reduces errors and improves overall efficiency.
Impact on Tone and Context: PLM fosters a collaborative tone within teams, promoting open communication and shared responsibility. The clear context provided by a centralized data repository minimizes misunderstandings and fosters a more efficient and harmonious work environment.
Exploring the Depth of PLM
A Brief History of PLM: PLM's evolution reflects the broader shifts in manufacturing and technology. Early PLM systems were largely focused on managing CAD data. However, over time, they evolved to incorporate broader functionalities, integrating various aspects of the product lifecycle. Key milestones include:
- Early Days (1980s-1990s): Focus on CAD data management and basic collaboration tools.
- Rise of Enterprise PLM (2000s): Integration of various aspects of product development, including manufacturing, supply chain, and service.
- Cloud-Based PLM (2010s-Present): Shift towards cloud-based solutions, enhancing accessibility, collaboration, and scalability. The rise of IoT and AI further integrates data analysis and predictive capabilities into PLM systems.
Core Components: A robust PLM system typically includes:
- A centralized data repository: A single source of truth for all product-related information.
- Workflow management tools: Automated processes to streamline tasks and improve efficiency.
- Collaboration tools: Enabling communication and information sharing across teams and departments.
- Reporting and analytics: Providing insights into product performance, costs, and overall efficiency.
- Integration with other enterprise systems: Connecting PLM with ERP, CRM, and other business systems.
In-Depth Analysis: Real-world examples of PLM's impact are abundant. Companies using PLM have reported significant improvements in:
- Reduced product development time: Streamlined workflows and improved collaboration accelerate the product development process.
- Lower product costs: Efficient design and manufacturing processes minimize waste and reduce overall costs.
- Improved product quality: Enhanced collaboration and data management reduce errors and improve product quality.
- Increased customer satisfaction: Faster time-to-market and improved product quality lead to increased customer satisfaction.
- Enhanced regulatory compliance: PLM systems help companies meet various regulatory requirements and avoid costly fines.
Interconnections: PLM complements other enterprise systems such as Enterprise Resource Planning (ERP) and Customer Relationship Management (CRM) systems, creating a holistic view of the business. Integration with ERP systems provides a seamless flow of information between design, manufacturing, and finance, while CRM integration ensures customer feedback is incorporated into the product development process.
FAQ: Decoding PLM
What does PLM do? PLM provides a holistic framework for managing the entire lifecycle of a product, optimizing every stage from concept to disposal.
How does it improve efficiency? By streamlining workflows, enhancing collaboration, and providing a single source of truth for product information, PLM dramatically improves efficiency.
Is PLM suitable for all businesses? While most beneficial for larger enterprises with complex product development processes, scaled-down versions or cloud-based solutions are increasingly accessible to smaller businesses.
What are the potential drawbacks of PLM? Implementation can be costly and time-consuming, requiring significant investment in software, training, and process changes. Data migration from legacy systems can also be challenging.
Practical Tips to Master PLM
Start with the Basics: Define your business needs and choose a PLM system that aligns with those needs.
Step-by-Step Application: Implement PLM in phases, starting with key areas and gradually expanding its functionality.
Learn Through Real-World Scenarios: Leverage case studies and best practices to understand how other companies have successfully implemented PLM.
Avoid Pitfalls: Thoroughly plan implementation, address data migration challenges, and provide adequate training to users.
Conclusion: Product Lifecycle Management (PLM) is more than a software system; it's a strategic approach to product development that drives innovation, efficiency, and market leadership. By mastering its nuances, businesses unlock new possibilities for growth and success in today's competitive landscape.
Closing Message: Embrace the transformative power of PLM and embark on a journey of streamlined product development, reduced costs, and enhanced customer satisfaction. The future of manufacturing is integrated, efficient, and driven by the power of PLM.
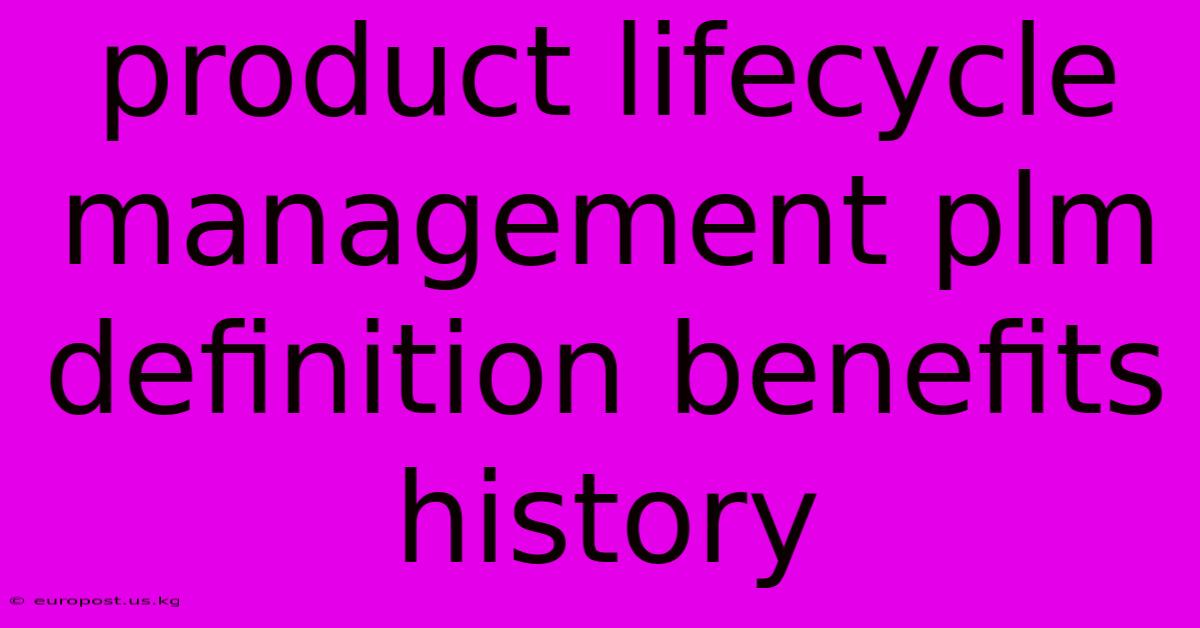
Thank you for taking the time to explore our website Product Lifecycle Management Plm Definition Benefits History. We hope you find the information useful. Feel free to contact us for any questions, and don’t forget to bookmark us for future visits!
We truly appreciate your visit to explore more about Product Lifecycle Management Plm Definition Benefits History. Let us know if you need further assistance. Be sure to bookmark this site and visit us again soon!
Featured Posts
-
What Is Private Credit
Jan 21, 2025
-
What Is Federal Benefit Credit
Jan 21, 2025
-
What Is Unsecured Credit
Jan 21, 2025
-
Unofficial Strike Definition
Jan 21, 2025
-
Blocked Currency Definition
Jan 21, 2025